Advanced Welding WPS: Customizing Specs for Complicated Projects
Advanced Welding WPS: Customizing Specs for Complicated Projects
Blog Article
Grasping Welding WPS Requirements: Best Practices and Techniques for Top Quality Welds
In the realm of welding, grasping Welding Procedure Spec (WPS) criteria is a vital component that directly influences the top quality and stability of welds. As we browse with the complexities of welding WPS standards, discovering key insights and approaches for attaining top-tier welds will be critical for welders looking for to excel in their craft and create welds that stand the examination of time.
Recognizing Welding WPS Criteria

Comprehending WPS criteria is crucial for engineers, welders, and inspectors included in welding operations. By adhering to WPS guidelines, welders can generate welds that satisfy the called for mechanical homes and structural honesty. Examiners rely upon WPS documentation to validate that welding procedures are being complied with correctly and that the resulting welds are of premium quality. Engineers use WPS criteria to make welding treatments that make sure the sturdiness and dependability of bonded structures.
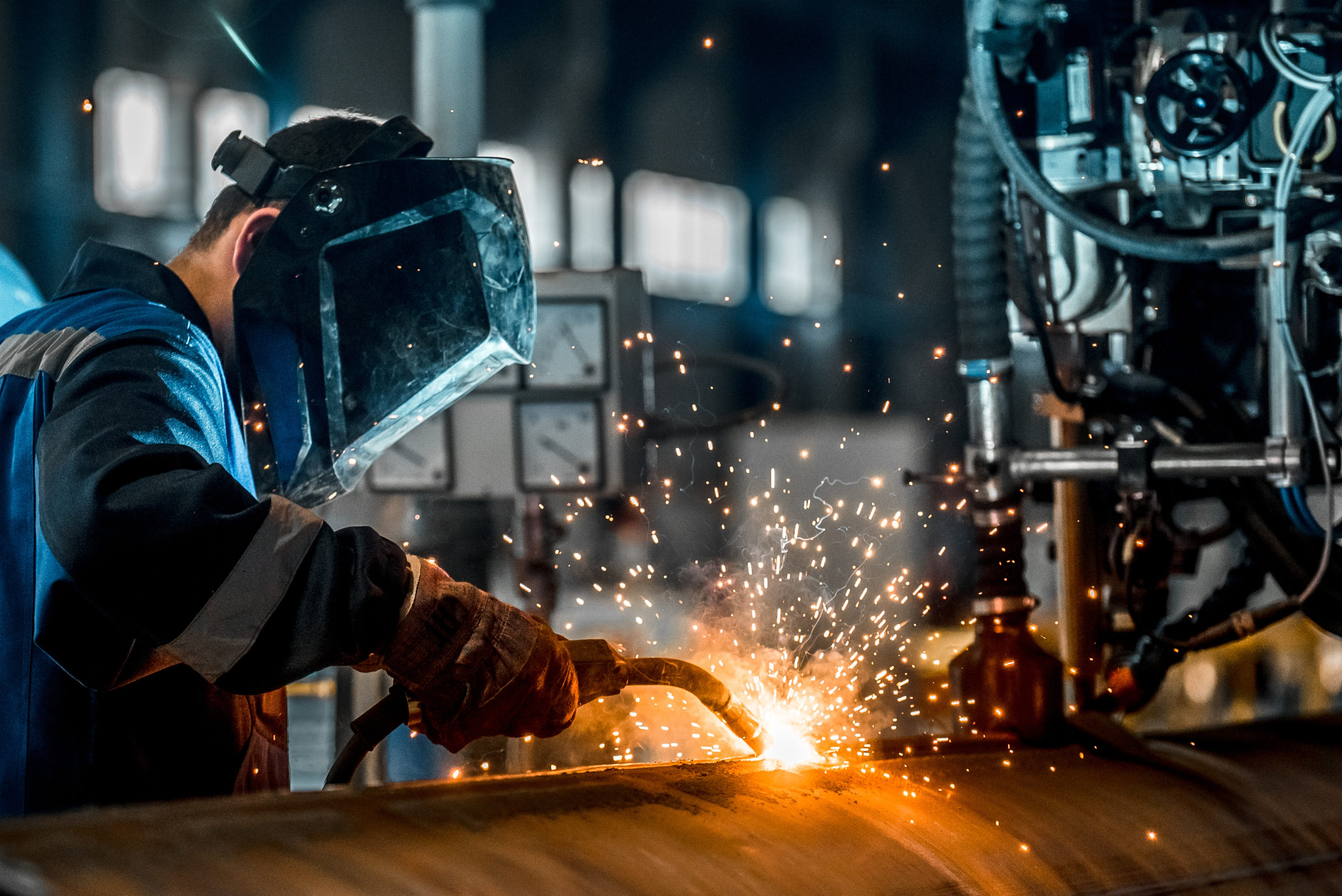

Important Tools for Top Quality Welds
Mastering welding WPS criteria is crucial for welders to successfully utilize the important tools required for creating high quality welds. One of one of the most essential tools for high quality welds is a welding equipment. The kind of welding machine needed depends on the welding procedure being made use of, such as MIG, TIG, or stick welding. Welding helmets are likewise important to safeguard the welder's eyes and face from sparks, heat, and UV radiation. Additionally, welding gloves made from heat-resistant and resilient materials guard the hands from injuries and burns. Magnets and clamps help hold the work surfaces together safely throughout the welding process, making certain exact and accurate welds. Wire brushes and breaking hammers are vital for cleaning the weld joint prior to and after welding to remove any pollutants that might affect the high quality of the weld. Lastly, a determining tape and angle mill work tools for ensuring correct alignment and preparing the workpieces for welding.
Key Methods for Welding Success
To attain welding success, one should grasp the key methods necessary for producing top notch welds. Preserving a steady welding and a steady hand placement throughout the procedure is essential to accomplishing accuracy and uniformity in the welds. By mastering these vital techniques, welders can elevate the quality of their job and accomplish welding success.
Ensuring Conformity With WPS Standards
Moreover, webpage welders should go through training to acquaint themselves with the WPS standards pertinent to their job. Regular audits and evaluations must be performed to validate that welding tasks align with the prescribed WPS guidelines. Furthermore, maintaining comprehensive records of welding parameters, tools calibration, and inspection outcomes is vital for demonstrating conformity with WPS criteria - welding WPS. By faithfully adhering to WPS standards, welders can ensure that their job fulfills the needed high quality levels and adds to the overall success of the welding project.
Troubleshooting Common Welding Issues
When encountered with typical welding issues, identifying the source is essential for effective troubleshooting. One common problem is the presence of porosity in welds, commonly created by impurities such as oil, rust, or moisture. To address this, making certain appropriate cleaning of the base steel prior to welding and using the correct securing gas can significantly decrease porosity. One more issue regularly come across is absence pop over here of blend, Your Domain Name where the weld falls short to properly bond with the base product. This can come from inadequate warm input or improper welding method. Adjusting parameters such as voltage, cable feed rate, or travel rate can assist boost fusion. In addition, distortion, breaking, and spatter are typical welding difficulties that can be reduced via proper joint preparation, constant warmth control, and choosing the suitable welding consumables. By completely comprehending these common welding issues and their source, welders can successfully repair issues and accomplish top quality welds.
Conclusion
To conclude, grasping welding WPS requirements calls for a complete understanding of the guidelines, using important devices, and executing crucial techniques for successful welds. Making certain compliance with WPS criteria is essential for generating quality welds and preventing usual welding issues. By adhering to best strategies and techniques, welders can achieve constant and dependable outcomes in their welding jobs.
In the realm of welding, mastering Welding Treatment Requirements (WPS) standards is an important part that straight influences the top quality and stability of welds.When delving right into the realm of welding practices, an essential facet to comprehend is the relevance and complexities of Welding Treatment Spec (WPS) criteria. WPS criteria supply a detailed guideline for welding operations, making certain uniformity, quality, and safety and security in the welding process. The kind of welding maker needed depends on the welding process being used, such as MIG, TIG, or stick welding.Achieving welding success via the proficiency of vital techniques demands a detailed understanding and adherence to Welding Treatment Requirements (WPS) standards.
Report this page